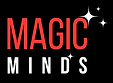.png)

WHAT IS BUSINESS IMPROVEMENT?
Every organisation will move through cycles of growth, change and challenges.
In order to strive for success and excellence, a focus is required on continuous improvement and alignment of purpose, people and processes.
Business improvement involves identifying, analysing, and implementing strategies to enhance various aspects of a business, such as efficiency, productivity, quality, customer satisfaction, and profitability. It focuses on optimising processes, workflows, and systems to achieve better outcomes and overall success for an organisation.
Ensuring your transformation program engages all employees and stakeholders is crucial in improving your chances of sustainability and success.

CASE STUDY
CONTINUOUS IMPROVEMENT PROJECT (2020 - 2021)
Working with one of the nation's favourite dairy brands, sourcing milk from 1,300 farmers in Britain in order to develop, manufacture, and market, a wide range of branded and private-label dairy products for the UK market, and using our expertise in Business Improvement and Continuous Improvement, we completed a 12-month engagement - recovering the business over £900,000 in lost profit.
Working with the production teams, we were able to assist in multiple efficiency improvements to production lines. One key project completed during this time was a short burst Kaizen Event that was aimed at investigating, yield, and the process of turning milk, amongst other ingredients, into yoghurt. During this event, we led a multifunctional team of 13 - comprised of production operators and leaders. Following the Define, Measure, Analyse, Improve, and Control method, the team worked together, facilitated by us, to develop the Kaizen scope. These objectives included:
-
Identifying all areas of yield loss throughout the production process.
-
Completing improvements to reduce areas of yield loss.
-
Producing a simple automated method to complete the mass balance of all batches produced.
-
Generating a fixed loss value for all processes in the yoghurt manufacturing process.
-
Producing a consistent and accurate method of recording process waste.
The current situation had shown that year-to-date, £202,000 was lost in yield, with a monthly average loss of £25,000 at a percentage of 2.65%. There was also no understanding of fixed losses on each process step. In addition, it was noted that potential savings, if a 50% reduction was achieved, would be circa £151,200 per year, with the industry-standard milk loss of 2%, equaling a potential saving of £75,640 per year.
After using process mapping techniques, analysing, measuring data, and inputting improvements from the process, the team were able to show substantial improvements, which equated to just over £433,000 in cash saving per annum.
Over the course of the 12 month program, we accredited 22 employees to Lean Six Sigma Green Belt level and facilitated 11 key projects, which saved the company over £900,000 in tangible savings by the removal of process waste and improvements linked to machine reliability.

Not sure what's right for your business? We encourage you to approach us directly with your specific requirements. If you're unsure if a business improvement project is the way forward for your organisation, you're welcome to join us for a no-obligation Teams call or in-person meeting to discuss your options.
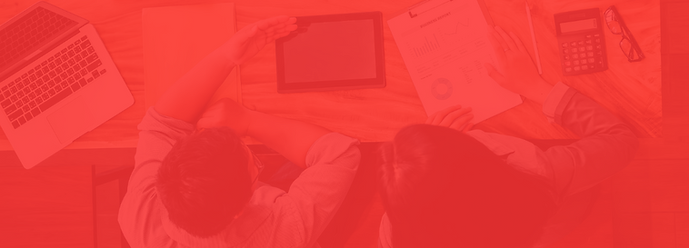
